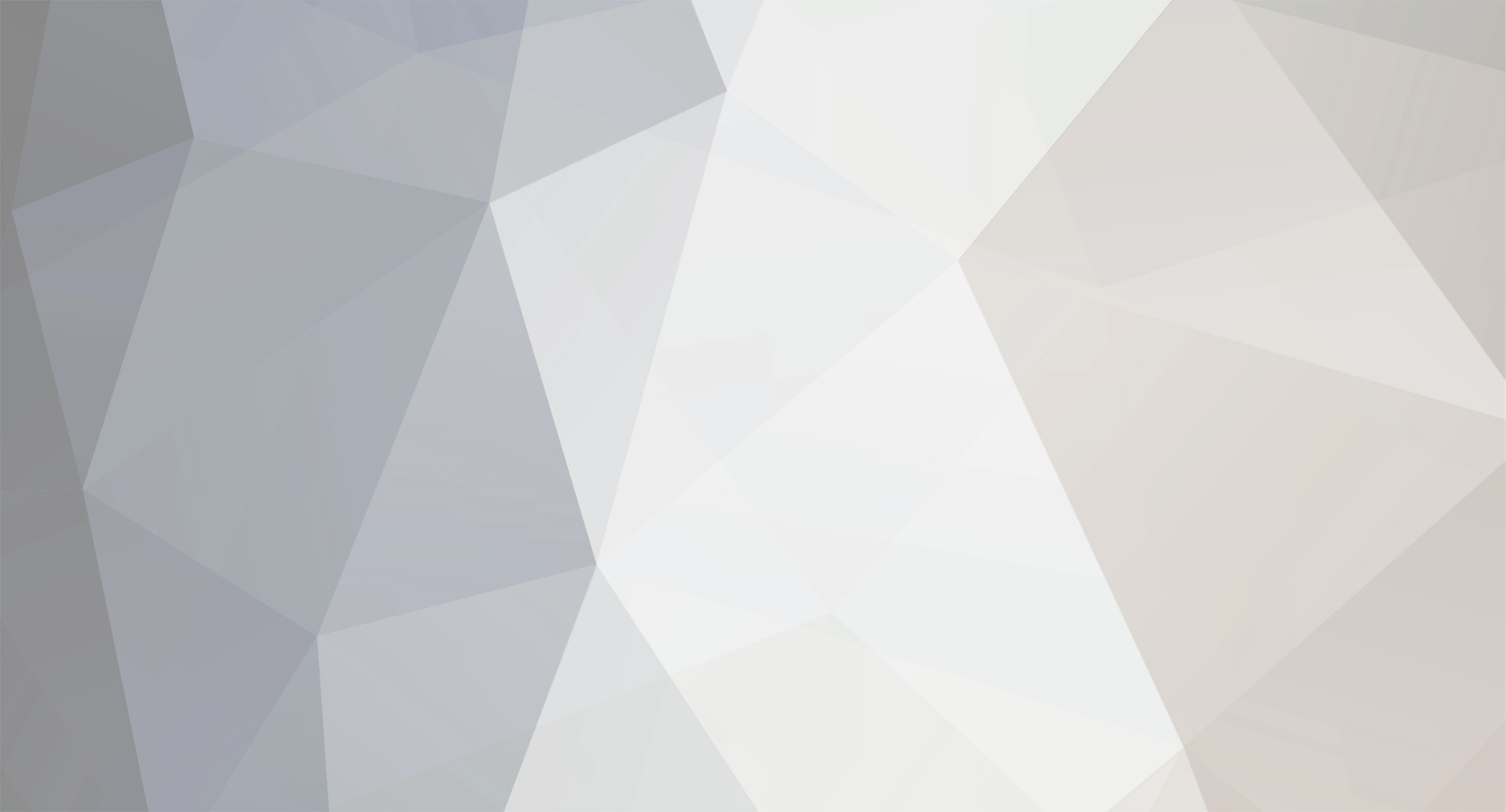
bobonikolov
Members-
Мнения
102 -
Присъединил/а се
-
Последно посещение
-
Days Won
6
Тип съдържание
Профил
Форуми
Календар
Всичко публикувано от bobonikolov
-
Братчедите на Steed - Chevy Colorado и GMC Canyon
тема отговори на bobonikolov's bobonikolov в Общи приказки
Ето колко са безполезни: https://www.youtube.com/watch?v=FIoahPvQ2II https://www.youtube.com/watch?v=a91LFp7eykA https://www.youtube.com/watch?v=TwLjoKIlkVA -
Вярна е наполовина. Наистина са съкратили около 60 човека и има спиране. Но не е заради нормите. От Great Wall коментираха пред Automedia.bg, че наистина има спиране на производството, но то е временно. Причината са множеството коли на склад, както и процесът по подготовка на конвейера за новата гама моделина марката, които видяхме на салона в София. Въпросните нови модели покриват нормите на Евро6. Към момента няма яснота кога точно ще бъде възобновено сглобяването на коли. От Great Wall бяха категорични, че заводът няма да бъде закрит. Потвърдиха обаче също така, че информацията за съкращаването на персонала е достоверна. От компанията допълниха, че продажбите им в България през 2015 година са били с 4% по-високи спрямо предходната година. Така пазарният дял на Great Wall у нас достига 2,12%. Припомняме, че заводът в Ловеч бе открит през февруари 2012 година. Към момента сглобените в България коли се пласират на няколко европейски пазара, сред които Италия, Румъния, Македония и Сърбия. Аз не мога да разбера само дори и да подновят производството как ще работят като са съкратили една четвърт от персонала. Нещо гнило има в Ловеч, но скоро ще се разбере какво.
-
Ето малко инфо за американските братчеди на Steed: 2012 Chevrolet Colorado – 2012 Chevrolet Colorado 3LT Crew Cab Pickup Interior 2012 GMC Canyon – 2012 GMC Canyon SLE Regular Cab Interior Излиза, че Steed си има и американски братчеди освен Исузу D Max. Сетих се за това, защото видях днес един Колорадо на магистралата и видях убийствената прилика отвътре и отвън. И двата са оборудвани с 2,9 литрови бензинови двигатели, Стандартното оборудване включва: CD player, MP3 аудио система с 6 високоговорителя, Bluetooth, Speed sensitive volume control, Sirius XM сателитно радио, окабеляване за телефон, OnStar система за навигация, климатик, часовник, компас, система за налягане в гумите, термометър, чупещ волан с кожа и т.н.
-
От опита като шофьор, който имам до момента мога да твърдя, че ос на колело се чупи изключително трудно дори и материала, от който е направен да е с лошо качество. Причината е проста - колкото и да е слаб чугуна или стоманата, от която е направена оста трябва първо да се появи пукнатина, която да доведе до счупването в крайна сметка. А това зависи най-вече от това как се кара един автомобил. Другата причина, която може да доведе до това са резки температурни аномалии, при които метала първо се разширява (заради загряване) и после рязко се свива заради бързо охлаждане. Така се получава например ако оста е загрята в следствие на горещо време, продължително жофиране без почивка или поради друга причина и автомобила например премине през много дълбока локва, където има хладка вода. В случая господина говори за фабричен дефект. За да се говори за фабричен дефект въобще трябва да са налице множество случаи на повреда от този тип. А в неговите обяснения са посочени всичко на всичко два такива. В този случай няма как да се приеме за фабричен дефект при положение, че в заводите на Грейт уол са произведени ако не милиони бройки от този модел автомобил, то поне стотици хиляди и до момента такъв дефект не е имало. Ако го имаше Грейт уол биха постъпили както всички големи автопроизводители и щяха да изтеглят от пазара сериозен брой автомобили, а за продадените щяха да осигурят безплатна подмяна на въпросната част. Такава е практиката по целия свят. Аз съм склонен в случая да приема, че оста се е счупила заради други причини, а не проблем в метала. Под други причини разбирам шофиране по разбити пътища и въобще кофти шофиране на колата.
-
Някогашните автомобилни заводи в България - минало и настояще
тема отговори на bobonikolov's bobonikolov в Общи приказки
4. KTA Мадара груп С решението за създаване на завода за товарни автомобили “Мадара” е поставено официалното начало на българското автомобилостроене. Изграждането на предприятието започва с помощта на съветски специалисти край Шумен през 1954 г. При откриването му през 1957 г. то разполага с леярна, пресово-ковачен цех и механичен цех. Същата година там започва производството на авточасти, като клапани, валове и зъбни колела. В началото на 1960-те год. започва разширяване на завода, реорганизация на работата и създаване на поточни линии със съдействието на инженерен екип от автомобилен завод „ЗИЛ“, Москва. През 1963 г. е усвоено производството на предни мостове, а през 1965 г. и на задни мостове за камионите ГАЗ 51, като скоро след това в Шумен започват да се изработват и двигателни мостове за модерния ГАЗ 53А. Не след дълго тези продукти стават основен приоритет на завода и на практика заемат около 50% от неговия производствен капацитет. В началото на 1966 г. е взето решение в завод “Мадара” да започне монтажа на съветските камиони ГАЗ. По това време, освен предни и задни мостове, там се произвежда и самоходно шаси Тип 22 – универсален четириколесен трактор с малка мощност с товароподемност 1 тон. През май 1967 г. в Шумен е изработена първата серия от 5 камиона ГАЗ-53А (първоначално те са лансирани у нас под името Рила 7, но то не успява да се наложи в серийната продукция на комбината). По същото време се очаква пристигането на комплекти за монтаж на още 10 камиона, а до края на 1967 г. в завода са сглобени общо 200 броя Към 1968 г. от завода вече излизат по 200 камиона месечно, а през септември същата година в експлоатация влиза нов монтажен цех, разположен на площ от 80 декара. През септември 1969 г. завод “Мадара” дебютира на международния панаир в Пловдив, където показва четири модела – базовият ГАЗ 53А, два негови варианта (с удължено шаси и самосвал) и експериментален образец, снабден с дизелов двигател от 80 к.с., изработен по лиценз на Perkins във варненския завод за двигатели “Васил Коларов”. Заедно с тях на същия панаирен щанд са изложени и два камиона Skoda-LIAZ, чийто монтаж също е усвоен през следващата година в Шумен. През октомври 1969 г. от монтажния цех в Шумен излиза 5000-ят камион ГАЗ, сглобен в България. На 4 февруари 1970 г. Чехословакия и България подписват 10-годишен договор за сътрудничество в производството на товарни автомобили. Една година по-късно е подписана и дългосрочна спогодба между ДСО “Автопром” и Генералната дирекция на Чехословашките автомобилни заводи за производството на задни мостове на товарни автомобили. През 1980 г. КТА “Мадара” усвоява новия тип задни мостове МТ, с които е снабдена модерната серия 100 на LIAZ. Новият модел на LIAZ разполага с 6-цилиндров турбокомпресорен двигател с директно впръскване и две разновидности – МШ 637 и МШ 638, чиято мощност е съответно 270 и 304 к.с. Първите пробни серии от него напускат монтажната линия на “Мадара” към края на 1980 г. На 17 юли 1981 г. в Шумен е подписан нов договор за сътрудничество в областта на машиностроенето между Чехословакия и България, който обхваща периода 1981 –2000 г. Според него България става най-големия, а след 1983 г. и едниственият производител на предни, средни и задни двигателни мостове за товарните автомобили LIAZ. Там също така е предвидено до средата на 80-те години КТА “Мадара” да произведе около 130 000 моста за нуждите на двете страни и да сглоби 15 000 камиона, като 2000 от тях да бъдат от новия модел 100. Производството на така наречените “стари” шкоди от типа MTS е окончателно преустановено през 1988 г., като дотогава са сглобени само няколко малки серии от новия влекач LIAZ 100 471. През 1987 г. е усвоен монтажа на LIAZ 100 050, а една година по-късно в Шумен започват да се сглобяват и всички модели серията 110, като 110 010, 110 030, 110 850 и влекачите за международни превози 110 471 и 110 551, чиято максимална мощност достига съответно 290 и 305 к.с. В началото на 1989 г. “Мадара” усвоява производството на самосвалите LIAZ 150 260, а в края на същата година в комбината започват да се сглобяват и първите самосвали с двойно предаване от типа 151, както и първите 1000 броя от 2,5-тонния ГАЗ 66. От този период средното годишно производство в КТА “Мадара” включва около 3000 камиона ГАЗ 53А и още около 3200 броя LIAZ, като над 90% от детайлите на двата базови модела идват от заводите производители. В периода 1971-1975 г. КТА “Мадара” експортира за Чехословакия 10 800 моста от типа RT, а между 1976 и 1980 г. обемът на доставките достига 54 800 броя (в това число 2700 задни моста от типа МТ и 100). От 1978 до 1984 г. количеството на задните двигателни мостове доставени на LIAZ вече възлиза на 122 700 броя от типа RT, MT и 100. От самото начало на сътрудничеството с LIAZ през 1970 г. до април 1989 г., в КТА “Мадара” са сглобени повече от 27 000 камиона от чешката марка, както и над 19 000 шасита за нуждите на комбината за автобуси “Чавдар” в Ботевград. Малко известен факт е, че LIAZ взима активно участие и в строителството на завод “Васил Коларов” във Варна, където започва производството на дизелови двигатели по лиценз на английската фирма Perkins. През 1991 г. КТА “Мадара” се трансформира в акционерно дружество, а през 1999 г. комбинатът е приватизиран и 85% от него стават собственост на компанията SFK Ltd. По това време заводът разполага с няколко халета, които заемат 246 000 кв. м. и открита площ от още 710 000 кв.м. Тогава средната цена на един камион LIAZ-Мадара е около $ 55 000, но към 2000 г. тя е намалена със 7 до 10% в зависимост от типа на надстройката. Този стратегически ход за привличане на нови клиенти не довежда до очаквания резултат и производството на камиони в Шумен спада до критичното ниво от 40 броя, продадени за цялата 2000 г. По същото време производството на LIAZ 100 в Чехия е спряно. Заводът работи и до днес като основният му продукт са всички видове земеделски инвентар - плугове, фрези, цистерни, пръскачки и т.н. -
Някогашните автомобилни заводи в България - минало и настояще
тема отговори на bobonikolov's bobonikolov в Общи приказки
3. Завод КЕНТА - Омуртаг Акционерно дружество „КЕНТА”АД е създадено през 1962 год. Производствената дейност се развива в две основни направления - ремонт на автобуси и производство на нови автобуси - собствена разработка носеща марката „КЕНТА”. Целогодишно извършва транспортна дейност – обществен превоз на пътници. Дружеството е разположено на 164 000 кв.м. площ, от които 38 144 кв.м. производствени сгради, 5 216 кв.м. складови сгради, 2 400 кв.м. административни сгради, 120 000 кв.м. не застроени площи. Персонала на „КЕНТА”АД е 151 души, от които 126 души изпълнителен и 25 души технически и административен персонал.Финансовото състояние на дружеството е традиционно стабилно. Работи без кредити - само със собствени средства. Годишния обем на продажбите е 1996 хил. евро. Стойността на дълготрайните материални активи е 2 милиона евро. „КЕНТА”АД разполага със свободен новопостроен цех с площ 6,5 декара с три корпуса и всички необходими промишлени инсталации - електрическа, пневматична, газова, вентилационна, отоплителна, битова, изградени транспортни коридори, подемно транспортни съоръжения и площадки. Оборудването на пресозаготвителния цех дава възможност за изработване на всякакъв вид заготовки от ламарина с дебелина до 12 mm. Дружеството разполага със собствена парокотелна, компресорна и ацетиленова станция. Производството е осигурено със всички необходими машини, инструменти и приспособления: за монтаж на шасита, универсално оборудване за механична обработка, както и за обработка на листова стомана, заваръчни апарати за заваряване в среда от въглероден двуокис, апарати за плазмено рязане, за електро - и газопламъчно заваряване, ръчни инструменти - пневматични и електрически за изработване на всякакви каросерии, подемно - транспортна техника и други производствено – технически възможности.Разполага с оборудване и технологии за възстановяване на резервни части за транспортни средства. Наличие на собствен автотранспортен парк. Благодарение на инфраструктурата, висококвалифицирания човешки потенциал и традиции, „КЕНТА”АД има възможност да развива и редица други производствени и ремонтни дейности в областта на машиностроенето / производство на контейнери, европалети и други /. Продукти и прототипи на завода: “Чавдар”11М4 Мерцедес 0303 “АВИА”5LC Чавдар 11 М 4 Чавдар Б 14 - 20 Произвеждат се контейнери за отпадъци, оградки за автономност (за градинки) и т.н. Източник: kenta-bg.com -
Някогашните автомобилни заводи в България - минало и настояще
тема отговори на bobonikolov's bobonikolov в Общи приказки
2. Завод Балкан - Ловеч Завод „Балкан“ е машиностроителен завод в Ловеч. Собственост на завода е частно акционерно дружество Балкан. Тук са сглобявани: самолети : „Лаз“, „АВИА“, и „ДАР“ (1943-1954) ; автомобили : „Балкан“, „Москвич“ (1966-1990), „Пирин-Фиат“ (1966-1971) и Ван ГАЗ ; мотоциклети„Балкан“. Съдържание [скриване] 1 Производство на самолети 2 Нова структура и производства2.1 Мотоциклети и велосипеди 2.2 Леки автомобили 2.3 Пикапи и микробуси 2.4 Други автомобили 2.5 След 1989 3 Източници 4 Външни препратки Производство на самолети[редактиране | edit source] Основна статия: Държавна самолетна фабрика (Ловеч) През 1938 г. отпада 20-годишното ограничение, наложено от Ньойския договор, и българската войска получава правото да притежава бойни самолети. Командването на въздушните войски решава да създаде модерна самолетна фабрика, в която да се съсредоточи българското самолетостроене на едно място, като създаде център извън столицата, разработващ и произвеждащ летателни апарати, по качество и количество съответстващи на най-добрите европейски образци. Специална комисия избира терен за фабриката. В Ловеч новината за построяването на завод не е посрещната с въодушевление поради това, че ще бъдат изкупени земеделски земи за построяването на завода. С последователност и упоритост кметът убеждава гражданите, че такъв завод ще създаде работни места, ще издигне интелектуалното ниво на града. Протокол от заседанията още се съхранява в общината. Самолетните демонстрации, проведени на 5 юли 1939 г., са посрещнати топло от ловчанлии. Сградите се строят по проекти на полски инженери, строили подобни съоръжения в Полша. Новият завод за производство на самолети е наречен Държавна самолетна фабрика (ДСФ). [1] Лаз-7М В Държавната самолетна фабрика са произвеждани следните типове самолети. „ДАР-9“ „Синигер“ е произведен през пролетта на 1943 г. В 3 последователни серии са построени 40 броя самолети. „АВИА-135“, чехословашки изтребител — доставен на части. Монтирани, изпитани и са предадени 12 броя на Въздушните на Н. В. войски. „ДАР-10“ е замислен като дивизионен разузнавач. Неговата разработка е започнала в ДАР, но прототипът е изграден в ДСФ. Това е високоскоростен моноплан, маневрен, със сигурно управление, бързо набиращ височина. Инж. Петко Попганчев, който изпитва машината, свидетелства, че този самолет е по-бърз от „АВИА-534“, но при катастрофа в мъгла през 1942 г. прототипът е унищожен. „ДАР-10Ф“ е разработка на инж. Ц. Лазаров. С двигател „Фиат“ самолетът има скорост 460 km/h и притежава качествата на много добър многоцелеви самолет — за разузнаване, за щурмови действия, за бомбардиране (хоризонтално и с пикиране), за въздушен бой. Самолетът е изпитан от инж. Попганчев през март 1945 г. , но този самолет не влиза в серийно производство. „Лаз-7“ и „Лаз-7М“. Самолетът е конструиран от инж. Лазаров и колектива му от конструктори. Моноплан, долноплощник, предназначен за първоначално обучение и квалификация на щурмани и военни пилоти. Това е изключително успешен самолет и е най-масово произвежданият самолет в България — 160 броя „Лаз-7“ и 150 броя „Лаз-7М“. „Лаз-8“ е четириместно въздушно такси. Представлява моноплан долноплощник и е изработен само прототип в чест и като подарък от самолетостроителите на провеждащия се конгрес на Българската комунистическа партия през 1948 г. След края на Втората световна война Държавната самолетна фабрика (по-късно: Завод 14) в Ловеч остава единственото предприятие в страната, което произвеждасамолети, след като авиационната фабрика в Казанлък е пренастроена за друго производство през 1947 г. Паралелно с дейността на завода върви и обучението на авиоинженери в софийската Държавна политехника, което продължава до 1954 г. Тогава е взето решение за окончателно закриване на самолетното производство в България, в резултат на което много от младите специалисти, инженери, техници и добре обучени работници в Завод 14, решили да посветят живота си на авиацията, са поставени в почти безизходна ситуация. Сред тях е и инж. Димитър Дамянов, който още в началото на 1950-те години постъпва на работа в Ловеч именно като авиоинженер. Първоначалното преструктуриране на завода след 1954 г. е свързано с краткотрайното налагане на напълно неприсъщи производства. Тогава ръководството на бившата авиационна фабрика проявява твърдост и излиза от кризисното положение със собствена инициатива, която е предложена пред висшите инстанции. Предлагат в Ловеч да започне производството на автомобили и мотоциклети, за което фабриката разполага с нужния технически потенциал и има висококвалифицирани специалисти. Нова структура и производства[редактиране | edit source]От 1965 г. заводът носи името Балкан и в неговия състав са включени шест завода - за производство на автомобили, за двуколесни превозни средства, завод за механични изделия, чугунолеярен, за производство на пластмаси и каучук и инструментален завод. От 1971 г. като завод от системата на "Балканкар" произвежда детайли и агрегати за електрокарното и мотокарното производство на България. С промените в структурата през 1991 г. този промишлен център е регистриран като акционерно дружество с държавата като едноличен собственик. Основно производство на акционерното дружество е производството на мотокари, хидродинамични предаватели, двигателни мостове, резервни части и велосипеди. Дружеството е приватизирано по линия на масовата приватизация през 1997г. и "Напредък холдинг" притежава 44% от капитала. [2] Мотоциклети и велосипеди[редактиране | edit source] Основна статия: Балкан (мотоциклет) Мотоциклет „Балкан“ Леки автомобили[редактиране | edit source]Към края на 1950-те години в тази атмосфера на висока техническа култура и професионализъм се заражда идеята за разработка на български лек автомобил, като целта е евентуалното усвояване на това престижно и перспективно производство да оформи основния профил на бившата авиационна фабрика. Предварителната подготовка за създаването на първия прототип започва в края на 1958 г. По същото време в двора на завода има лек автомобил Volkswagen, чийто двигател и шаси са използвани за образец. Към процеса на предварителна подготовка се включват и специалисти от „Завод 12“ в София, които успяват да изработят абсолютно идентично и най-важното функциониращо копие на предоставения им оригиналендвигател (след 1956 г. производството на всички двигатели за мотоциклетите „Балкан“ е възложено именно на „Завод 12“). С оформянето на каросерията се ангажира екипът на инж. Дамянов, който по това време включва Юли Костов, инж. Кънчо Кънчев, инж. Иван Петров (заместник-главен инженер), Георги Филипов, Пейчо Пейчев, Георги Лазаров и още няколко души. Изковаването на отделните компоненти на каросериите от тънколистна ламарина се извършва изцяло на ръка, с помощта на дървени чукове върху кожени възглавници, пълни с пясък. „Москвич Алеко“ Модел 2141s Това, което особено затруднява екипа на инж. Дамянов, е така наречената „геометрическа разработка“, която се разчертава върху огромна маса в мащаб 1:1. Именно от нея впоследствие се свалят всички мерки за изработването на шаблони, от които пък се правят детайлите на дървения макет. Последният етап от работата е свързан с разрязването на дървения модел на отделни части, от които се отливат металните щампи за външните форми на каросерията. Основният отговорник по изработването на моделите е Марин Радев, а с изковаването на отделните външни елементи е натоварен Георги Лазаров. Пикапи и микробуси[редактиране | edit source]Паралелно с лекия автомобил е изработен и прототипът на лекотоварен автомобил, базиран на Volkswagen Transporter, чийто дизайн е почти идентичен с оригинала. През септември 1960 г. един от леките автомобили и пикапът са изложени на открита площ на територията на Международния мострен панаир в Пловдив с надпис „Произведено в България“. През пролетта на 1962 г. в Ловеч отново е поставен на обсъждане въпросът за евентуалното производство на лекотоварен автомобил. През март същата година колективът на инж. Дамянов започва предварителната подготовка по тази задача, като към първоначалната група се включват и Иван Савов, Васил Вълев, Богдан Хамбарджиев и инж. Любомир Тошев, който поема основната работа по окачването. Целта е до 6 месеца да бъдат напълно завършени прототипите на лекотоварен автомобил и микробусс идентична предна част, които да се представят на юбилейния 20-ти поред мострен панаир в Пловдив. През 1962 г. усилията на конструктивния отдел са насочени към създаването на лекотоварен автомобил с полезен товар 800 кг и малък автобус със 7+1 места на основата на съветските автомобили „Волга“ и „Москвич“. Пикапът е изцяло произведен в Ловеч, но за каросерията на 11-местния микробус е направено работно посещение в автобусния завод „Чавдар“, Ботевград, който тогава е единственото специализирано предприятие за производство на автобусни каросерии. Двата модела са показани в Пловдив през септември 1962 г. под името „Балкан Т800“, като тяхното представяне отново минава при огромен успех, подкрепен от няколко възторжени статии в наши и чужди специализирани издания. През април 1963 г. е завършена нулева серия от още 3 лекотоварни автомобила, чиято товарна платформа е направена от дърво за разлика от първия прототип, при който е метална. Изпитанията преминават успешно и предложеният план за серийно производство на „Т800“ е одобрен на най-високо ниво, но точно тогава възниква неочакван проблем — оказва се, че руснаците не могат да произведат достатъчно комлекти от шасита и двигатели (по това време „Москвич“ все още е единственият масов личен автомобил в СССР), а ограниченият производствен капацитет на завода далеч не покрива дори нуждите на местния пазар. Въпреки всичко проектантската дейност продължава и през 1965 г. заводът представя макет на нов, по-модерен вариант на микробус, а през 1966 г.-на фургон в мащаб 1:5, чието външно оформление е възложено на инж. Петко Мишев от Центъра за промишлена естетика и художествено проектиране (ЦПЕХП), който след 1964 г. разработва дизайна и на почти всички мотоциклети „Балкан“. През 1967 г. на Пловдивския панаир е показан прототипът на „Рила 700“-микробус, базиран на „Москвич 408“, чиято каросерия проектира Христо Христов-един от изтъкнатите архитекти на Ловеч. Последната серия макети на микробус „Рила“ са предложени през 1970 г. от Петко Мишев и Емил Иванов (един от водещите дизайнери на транспортни средства в ЦПЕХП), но и те не получават нужното одобрение от съответните инстанции, с което работата по прототип на български микробус е окончателно преустановена. Други автомобили[редактиране | edit source] Основна статия: Пирин-Фиат Основна статия: Москвич Алеко След 1989[редактиране | edit source]През 1995 е преобразуван в еднолично дружество с ограничена отговорност, а през 1996 в акционерно дружество. От 1997 Балкан е частно акционерно дружество 100 човека персонал. Днес някогашният автомобилен завод произвежда................ метални стилажи, палети и тръбна градинска мебел. В него работят 100 души, от които 20 са административен персонал. Голяма част от оборудването на завода е предадено за вторични суровини включително и цялата поточна линия, на която се е сглобявал "Москвич". -
В тази тема ще предоставям периодично информация за автомобилните заводи, които нашата страна е имала и какво е тяхното положение в момента. 1. Завод „Чавдар” в Ботевград – гордостта на родното автобусостроене През 1988 г. представителите на чуждите дипломатически мисии у нас воглаве с Тодор Живков, провеждат традиционната си лятна визитация из страната. Дипломатите посещават Правец и Ботевград, а с автобус родно производство Живков лично ги развежда между различните заводи, гордост за социализма – КМТ „Правец”, „Ботевградска вишна“, химическият комбинат „Пластхим“. Сред тях е и автобусния завод „Чавдар” в Ботевград – гордостта на родното автобусостроене. Ако днес Росен Плевнелиев реши да покаже на дипломатическия корпус някогашния Комбинат за автобуси “Чавдар”, те ще заварят там една прекрасна картинка на пустошта. Някогашният проспериращ завод, който е давал работа на над 2000 души тъне в печал и разруха. От скъпите конвейери и машини не е останала гайка. Огромните халета са полуразрушени, а около тях щъкат бездомни кучета. От години цигани денонощно рият и обезкостяват сградата, като изкопават основите й. По-възрастните жители на града буквално страдат за комбината. По кафенета и магазини се чува само едно: „Разграбиха го. До шушка.”! Историята на завода за автобуси “Чавдар” в Ботевград започва още от времето, когато селището се нарича Орхание. Даровитият майстор на шасита Рачо Джамбов създава коларо-железарска работилница през 1924 г. В края на 30-те години, когато е отбелязан най-благоприятният период от предвоенната история на работилницата, се изработват по две каросерии месечно, а работниците на Рачо Джамбов вече са повече от 15. До Втората световна война произвежда пътнически каросерии, които са толкова надеждни, че получава поръчки от Леон Арие, официалния вносител на “Мерцедес” за България, а за Дирекция на въздухоплаването конструира специални каросерии за самолети. По време на Втората световна война производството на каросерии е спряно, поради липса на шасита. Народната власт национализира работилницата му в края на 1947 г. и я нарича Автокаросерийна фабрика „Георги Димитров”. Джамбов остава на работа в своята фирма, като технически ръководител, а неговия племенник Рачо Христов Джамбов поема директорския пост. На 1 май 1948 г. е произведен първия следвоенен автобус, базиран на шаси Шкода RTO, като до края на същата година в Ботевград са комплектовани с пътнически каросерии още 3-4 четири платформи от същата марка. През септември 1948 г. една от каросериите е показана на Пловдивският мострен панаир, което е и първата подобна изява за автобусите, изработвани в Ботевград. В началото на 50-те години започва разширяване на предприятието, в резултат на което става възможен монтажа на пет автобуса едновременно. През 1955 година в каросерийната работилница постъпва на работа сина на Рачо Джамбов, Васил. В периода 1942 – 1944 г. той учи във Висшето политехническо училище в Мюнхен и се завръща в България като машинен инженер. След неговото присъединяване към все още скромния екип на работилницата са направени редица реорганизации, което от своя страна допринася за увеличаване на производителността до 150%. Пак по инициатива на Васил Джамбов е изработен прототип на 10-местен микробус, базиран на шаси Opel Blitz. Каросерията е копие на един от популярните по това време съветски модели, но благодарение на чертежите, които Джамбов изработва, каросерията е с около 200 кг. по-лека от оригинала. За съжаление някой от ръководните фактори по това време не желаят неговото присъствие в работилницата под предтекст, че „това не е най-удачното място за син на частник”. В резултат на оказания натиск тогавашният директор и добър приятел на Джамбов Петко Петков е принуден да го отстрани от работа само една година след неговото назначаване. В средата на 50-те години каросерийната фабрика в Ботевград е и единственото специализирано предприятия за производство на автобуси в България. През 1956 година „по предложение на работническия колектив”, предприятието за автобусни каросерии в Ботевград е наречено „Чавдар”. Две години по-късно е представен прототип на модерен автобус с вагонна каросерия, чието серийно производство е усвоено в края на 50-те години. През 1959 г. в Ботевград е изработен и прототип на луксозен туристически автобус, наречен „Чавдар-Туту”. Той се отличава с високото ниво на комфорт, панорамните стъкла, креслообразните седалки с променлив наклон, страничното изместване и други. След 1962 г. серийните модели М-65 и М-66, предназначени съответно за градски и междуградски превози вече се снабдяват с пневматичен автомат за отваряне на вратите, а обикновените стъкла са заменени със секуритни. От същата година датира и производството на малки автобуси, базирани на шаси от ГАЗ-51 със специфично оформена предна част, които стават популярни с името „Пионер”. До 1964 г. паралелно с автобусните каросерии в „Чавдар” се произвеждат машини за хранително-вкусовата промишленост, хладилници и т.н., но от средата на 60-те години чувствително разширената работилница се обособява, като специализирано автобусно предприятие. В края на 1966 г. в НИПКИДА (Научно-изследователски и проекто-конструкторски институт за двигатели и автомобили) в София започва проектирането на модерните автобуси Чавдар М80 и М81, които също са базирани на товарно шаси Skoda, а серийното им производство започва през 1968 г. и достига до 400-500 броя годишно. Художник-проектант на каросерията е инж. Борис Ачков. През 1968 г. е предприета радикална модернизация и разширяване на предприятието, както и подготовка за производството на изцяло нова, модерна каросерия по лиценз на Kaesbohrer. Договорът със западногерманската фирма включва разработване на документация и доставка на технологична екипировка за изработването на новите модели. Първите два прототипа са завършени и доставени в България още през 1970 г., но серийното им производство е усвоено едва през 1974 г. На външен вид това са почти идентични с актуалния по това време модел на Kaesbohrer “Setra”, но са адаптирани към шаси от Skoda с предно разположен двигател и различна като пропорции и междуосие ходова част. Това от своя страна налага цялостна преработка на каросерията, в резултат на което се получава един оригинален автобус, който няма аналог сред серийната гама на германската компания. Скоро след като влизат в серийно производство двата лицензни модела „Чавдар”11Г5 и „Чавдар” 11М3, предназначени съответно за градски и междуградски превози, се появява цяла серия от модификации и специални поръчкови изпълнения, като подвижна книжарница, подвижна приемна, стоматологичен кабинет, мебеловоз, флуорограф и др. През втората половина на 70-те, годишното производство достига 2800 броя, което от своя страна позволява част от готовата продукция да бъде пласирана в чужбина. След като завършва разширяването на предприятието, с 210-то разпореждане на Министерския съвет е взето решение да се извърши териториална концентрация и специализация на автобусното производство, като то се съсредоточи на територията на Ботевградската селищна система. Така през 1977 г. предприятието прераства в комбинат и освен завода в Ботевград включва още няколко съставни завода, като МЗ „Прогрес” – Етрополе, където се изработват части от скелета на автобуса, МЗ „Д. Грънчаров” – село Джурово, който се специализира в изработването на алуминиевите рамки за остъкляването и броните, МЗ „Гев. В. Марков” – Ябланица, производител и доставчик на дървената и металната част от седалките. МЗ „Възход” – село Трудовец, който изработва тапицерията и МЗ Ботевград. По това време един автобус „Чавдар” се състои от 45 000 детайла, а личния състав ангажиран във всички фази на производствения процес възлиза на 1850 човека. Пак през 1977 г. е усвоено и производството на самоносещите автобуси „Чавдар” 11М4, което е вторият етап от лицензния договор с Kaesbohrer. Моделите 11М4 вече са със самоносеща каросерия и техните разновидности изцяло повтарят външните линии на германските оригинали, но се предлагат с чешки двигатели от LIAZ, както и унгарски RABA-MAN. Те са снабдени с така наречената „въздушна възглавница”, произвеждана по унгарски лиценз, благодарение на която комфортът на возене е многократно подобрен. По време на специализираното международно изложение на туристически автобуси през 1977 г., проведено в Дубровник, тогавашна Югославия, „Чавдар” 11М4 получава трета награда. Същият модел се завръща със златни медали и след своите участия на международните панаири в Пловдив и Бърно, Чехословакия през 1978 г. През този период автобусите „Чавдар” вече се експортират в Афганистан, Никарагуа, Северна Корея, Гърция, СССР и др. Интересно е да се отбележи, че още през 1968 г. е създадена База за техническо развитие на автобусите (БТРА), която след време прераства в институт. През 70-те и 80-те години именно там са конструирани множество прототипи, част от които впоследствие са внедрени и в серийно производство. По-известните от тях са „Чавдар” 5С-1 – първият в света сериен микробус тип 4х4, модерните градски автобуси В14-20 (В13-20), микробусът LC-51, базиран на шаси Avia, а също така тролейбуси, съчленени автобуси и др. Високопроходимият „Чавдар” 5С е проектиран от инженерите Кирил Хаджиев и Любомир Тошев в края на 70-те години, а първата експериментална серия от 16 шасита е готова през 1979 г., когато са демонстрирани и няколкото завършени прототипа. Серийното производство на 5С е усвоено около две години по-късно и продължава до средата на 90-те години. Първоначалните планове са 5С да бъде лансиран с изцяло нов дизайн, чието проектиране е поверено на инж. Петко Мишев от Центъра по промишлена естетика. Модерните прототипи са изработени в единични бройки, които представят няколко различни модификации – лекотоварен, фургон, микробус и дори военен автомобил. За съжаление ръководството в Ботевград предпочита да се придържа към класическия външен вид на „Чавдар” и за това серийния 5С напрактика представлява умалено копие на автобусите произвеждани в комбината. Подобен е и случая с микробусът LC-51, базиран на Avia, който въпреки предложения модерен вариант (проектиран отново от инж. Мишев) не успява да се откъсне от наложенената модна линия. Основната разлика между него и стандартните автобуси може да се открие единствено в наличието на вертикално разположените и различни по форма стоп-светлини. Един от големите успехи на „Чавдар” в чужбина е свързан с модерния градски автобус В14-20, представен през 1981 г. Неговото проектиране започва в резултата на един международен конкурс, обявен от общината на град Атина за доставката на 200 пътнически автобуса, които да заменят остарелия автопарк на града. Въпреки силната конкуренция от страна на извени западни компании, конкурсът е спечелен от „Чавдар”, а дизайнът на новия модел, наречен В14-20, отново е дело на инж. Мишев. За добре свършената работа Петко Мишев и още двама конструктори от завода са наградени лично от Тодор Живков с командировка в германските автобусни заводи Kaesbohrer, Neoplan и Mercedez-benz. В началото на 80-те в предприятието са правени опити и за производство на тролейбуси върху шаси от автобус, но в случая може да се говори по-скоро за единични бройки, а не за серийно производство. Произведени са два тролейбуса, които са се движили по линиите на градския транспорт в Пловдив. През 1984 година е закупен лиценз от австрийската фирма Steyr-Daimler-Puch за производство на фамилия линейни автобуси - градски „Чавдар” – 130, крайградски „Чавдар” – 330 и съчленен градски автобус „Чавдар” – 140. Новите модели са усвоени през 1988 г., когато е завършена първата производствена серия от 10 автобуса, оборудвани с агрегати LIAZ. През същия период са изработени опитно образци и малки серии от новата фамилия междуградски и туристически автобуси „Чавдар” 410, 420, 430 и 530. Чавдар 530 е един от най-луксозните автобуси, произвеждани в завода. От него са произведени няколко броя. Негов еквивалент е Setra S215 HD. Пак през 1984 г. „Чавдар” и унгарския производител на автобуси Ikarus създават съвместен прототип на съвременен 8-метров автобус с 30 места. Двата завършени екземпляра са изработени в Секешфехервар, Унгария, като единият остава там, а другият идва в България, където преминава серия от изпитания. Предвиждало се е автобусът да бъде произвеждан серийно за пазарите на социалистическите страни, но тази идея остава нереализирана. След 1989 г. поръчките към „Чавдар” рязко спадат и предприятието започва да търси начини да се ориентира в новата пазарна среда. През 1993 г. комбинатът сключва договор с германската компания "ЩАЕР Даймлер Пух", за сътрудничество в развитието, производството и продажбите на автобуси „Чавдар”, в резултат на което се появява новият съчленен градски автобус „Чавдар - 141”. През октомври същата година този модел участва в търг за модернизиране на градския транспорт, организиран от Столична община, а негови конкуренти са такива изтъкнати производители, като Mercedes-benz, Sanos, Ikarus, Scania, Van-Hool и Skoda. „Чавдар” печели конкурса, но кмета Янчулев обявява завода за пропаднал и умишлено протаква сделката, като без сериозни аргументи отказва да бъдат закупени поръчаните 60 автобуса. "Ние престиж на този завод няма да създаваме. Не може при съществуващата финансова криза на общината от парите на данъкоплатците, които формират бюджета в София, да се финансира подобна сделка само заради съживяване на родното производство". Това решение в известна степен също спомага за по-бързото ликвидиране на завода. Чавдар 610 е последният модел, изработен в завода преди той да бъде окончателно закрит. Моделът е изгладен на шаси AVIA- DAEWOO А65. Броят на седящите места е 26(25)+1. Пътниците са повече от тези при ЛС-51, защото използваните седалки са с ширина 400mm и на ред са по 4 седалки, за разлика от ЛС-51, при който седалките са 3 на ред и с ширина 480 mm (каквато е и стадратната ширина за всички останали автобуси). Новото при този модел е, че вече се появява лепено остъкляване и автобусът е облицован със стъкло-пластмаса, също така е оборудван с климатик. В началото на 1999 г. финансовото състояние на предприятието е твърде нестабилно. През февруари същата година в медиите е публикувано съобщение, според което една американска компания проява интерес към евентуалното приватизиране на „Чавдар” ЕАД. Обнадеждаващите перспективи обаче са помрачени на 17 Март 1999 г. със заповед №108 на финансовият министър Муравей Радев, която официално обявява завода в ликвидация. Предприятието е приватизирано по порочната схема на т.нар. РМД (работническо-мениджърско дружество), след което започва и неговата ликвидация. Идеята е ликвидацията да приключи до 30 юни и с това да се даде възможност на 755-те служители да закупят отделни активи от предприятието. Активите му са разпродадени, след последвала неколкократна смяна на собствениците. Гордостта на родното автобусостроене, не без „помощта” на властимащите отива в историята. Финансистите обясняват, че фалитът е бил неизбежен, поради огромните дългове, натрупани от предприятието, които в края на 1998 г. възлизат на 20,8 милиарда (инфлационни) лева. През март 2001 г. отново настъпва известно оживление, тъй като две компании от Германия и Близкия Изток проявяват интерес към купуването на „Чавдар”, но до съживяване на производството така и не се стига. Източник:socbg.com Днес бившият завод Чавдар тъне в разруха: https://www.youtube.com/watch?v=uRhZ4VttV3c
-
Нова фабрика за тапицерии за Мини Купър в България
тема отговори на bobonikolov's admin в Общи приказки
Чудесно. Доколкото разбрах догодина предстои да започне и фаза 2 в Ловеч, а именно изграждане на цех заваръчен и цех бояджийски. Стане ли това остава да се започне развойна дейност за собствени автомобили, защото около 25 000 души в България работят в производството на авто компоненти. Ето повече инфо за преприятията тук: Източник: http://www.24chasa.bg/Article.asp?ArticleId=4097211 -
Много добнре е направен последния репортаж. Но от клиповете се виждат няколко неща, които трябва да се оптимизират на поточната линия за по - бърза сглобка и по - удобна работа на работниците: 1. В началото на сглобяването, когато има само голо купе във доста заводи по света вратите се свалят и поемат по отделна поточна линия, където се оборудват и сглобяват като идват до автомобила в самия край на поточната линия, където само ги закачват. През това време работниците без никакви проблеми вкарват и монтират таблото и седалките с роботи. 2. Както казах вече работниците трябва да монтират седалките и таблото с помощта на помощни роботи, които да поемат тежестта им. Представете си иначе какво ще стане ако един работник вдига всеки път и носи до клата седалки ако капацитета стигне няколко хиляди автомобила годишно и на всеки пет минути по линията минава кола. Ще му се съсипе кръста, гърба, ставите и много други неща. 3. При монтажа на гърнетата, маркучите и всякакво окабеляване от външната страна на пода на колата в много заводи купето се завърта на 90 градуса на поточната линия за да може работникът да монтира съответните части отново с помощта на повдигачи докато е прав и да не се налага да кляка всеки път или да се навежда всеки път. 4. При монтажа на гумите автомобила трябва да е на височина поне 1,5 метра, а работникът да поставя гумите с помощта на повдигач и да ги монтира с пистолета на сгъстен въздух, а не както сега колата да е на 20 см от земята, а едно момче да се навежда и да вдига гумите на ръка. Мотивите - отново ако се налага да го прави по 1 000 пъти на ден ще си съсипе здравето. Въобще има доста неща, които трябва да се оптимизират за по - добра работа.
-
"Видях Great Wall" - къде и кога? Ако може и снимка :)
тема отговори на bobonikolov's feikot в Общи приказки
Вчера, 10.05 - Steed 5 на летище Хийтроу в Лондон. За съжаление бях с гръб към предната част на автобуса и не успях да го снимам :-) -
Да така е съгласен съм. Един пример. Забелязах, че в Ютюб има клипове от завода на Грейт уол в Китай, където се организират туристически обиколки на завода със специални влакчета. Влакчетата тръгват от паркинга на завода и обикалят по определен маршрут вътре в него. Никъде не се пуска без контрол. Но твърденията на няколко индивида под статията определено дразнят. А и като знам, че има хора които са наивни и вярват на всяка дума колко му е да тръгне лош слух за завода.
-
Времето ми е много уплътнено иначе с удоволствие бих се възползвал :-D
-
Капацитетът на завода е увеличен двойно, продукцията ще се реализира на европейските пазари Най-новият модел, който сглобяват в Ловеч - Great Wall H6. Снимка: Automedia.bg В ловешкия автомобилен завод ще произведат своя 5-хиляден автомобил до края на тази година, съобщи пред БТА изпълнителният му директор Андон Димитров. За малко повече от две години, откакто е започнало производството край Ловеч, са сглобени около 2500 автомобили на китайската марка Great Wall, реализирани основно на българския пазар. През следващите години обаче компанията ще стъпи на нови пазари, което налага увеличаване на производствения капацитет на предприятието. От декември миналата година заводът изнася своя продукция на пазара на Италия, за където пътуват по около сто автомобила на месец. Компанията изнася и за Македония, а до края на годината се очаква да стъпи на пазарите в Сърбия, Румъния, Унгария и Словакия. През 2016 година продукцията на завода трябва да бъде налична на общо 16 европейски пазара. Директорът на компанията "Литекс моторс" Илия Терзиев каза, че целта е марката да се утвърди на българския пазар и припомни, че през февруари тази година са предоставили 27 автомобила Great Wall H6 на пожарните в страната, а в края на март - 51 пикапа Steed 5 на Министерството на околната среда и водите. Илия Терзиев съобщи също, че целта е до 4-5 години компоненти за автомобилите да се произвеждат и доставят от български фирми. В момента сглобяваните в Ловеч автомобили използват български акумулатори, масла и течности. Вече са водени преговори с български компании, както и с ръководството на завода за автомобили.
-
Произвежданият в България модел вече се продава в страни от ЕС През поточните линии на завода за автомобили в Ловеч, който бе открит преди две години, вече минаха четири различни модела на китайската марка Great Wall. Петият - H6, който се качи на конвейера наскоро, е моделът, на който производителите възлагат най-големи надежди. Именно той трябва да отвори пазарите на Европа за Great Wall. Едни от първите автомобили Great Wall H6, произведени в Ловеч Още при първата копка на завода беше ясно, че продукцията му ще бъде предназначена за Европа. Все пак пазарът на България е прекалено малък за капацитета на цял автомобилен завод. Износът на сглобяваните до момента модели - Voleex С10, Hover H5, Steed 5 и Voleex C20R, достигна най-вече до съседните на България страни. Плановете за напълно новия H6 обаче са далеч по-смели. Предвижда се моделът да стъпи на пазарите на Сърбия, Румъния, Чехия и Унгария още преди края на 2014 г. А до 2016 година да бъде наличен на общо 16 европейски пазара, сред които Италия, Чехия, Словакия, Словения, Унгария, Полша, Австрия, Румъния, Албания, Гърция и дори Турция. Става въпрос за сглобени в България автомобили. Всъщност износът на Great Wall H6 вече започна. Моделът бе представен в Италия, от където дойдоха и първите 200 заявки. Предварителните планове сочат, че към страната ще пътуват по около 150 автомобила на месец. При интерес, износът ще бъде увеличен. Това са европейските пазари, на които H6 трябва да се продава до 2016 г. В момента във фабриката на Литекс Моторс край Ловеч работят около 200 човека. Предвижда се обаче броят им да расте всяка година, като при пълен производствен капацитет от 50 000 автомобила годишно, заетите в завода може да достигнат 2 000 души. Новите халета, които трябва да бъдат построени през следващите няколко години, ще бъдат предназначени за точково заваряване и боядисване. Една от станциите на поточната линия Защо обаче производителите са избрали именно H6 за свой посланик в Европа. Кросовърът е най-модерният и съвременен модел на Great Wall. Той е и най-продаваният SUV в Китай за 2013г., като получи титлата „4х4 автомобил на годината“ в страната. Моделът е и сред основните "виновници" за 48-процентното увеличение в продажбите на SUV автомобили, което Great Wall записа през 2013 г. Освен това търсенето на SUV автомобили в Европа непрекъснато расте. А заводът край Ловеч е избран, тъй като това е единственото автомобилно съоръжение на компанията, чиято продукция има типово одобрение и сертификация за производство и продажба на автомобили на територията на Европейския съюз. Освен това заводът на Литекс Моторс е отличен за най-добър завод на Great Wall извън Китай в две поредни години – 2012г. и 2013г. Не на последно място, заводът е избран и заради стратегическото разположение на България и сравнително евтината работна ръка. Great Wall H6 получи 5 звезди на китайските краш тестовете, което е най-високата възможна оценка Дали обаче Great Wall H6 е достоен за Европа? Това само времето може да покаже. Ние ще се постараем да изтъкнем предимствата и недостатъците на модела, които открихме за себе си. Great Wall H6 е изключително просторен и добре оборудван кросовър. Двигателят му е китайска разработка и се произвежда в Китай. Но компонентите са доставени и произведени от световни фирми. Същото се отнася и за системата за задвижване на четирите колела и цялата периферия на мотора. Двигателят, например, разполага с последно поколение DELPHI Common Rail система, VGT - турбо компресор с променлива геометрия от BorgWarner, последно поколение DPF филтър и EURO 5b+ ниво на вредни емисии. А за задвижването се грижи последно поколение advanced TOD® система за интелигентно 4х4 задвижване, разработена от американския гигант BorgWarner. Сред другите доставчици са компании като Valeo, Bosch, ZF, Johnson Controls, Mahle, Ricardo и др. Поредната проверка за качество Що се отнася до сглобката, за която отговарят българските майстори, тя е на много високо ниво. Екипът е млад - средната възраст на механиците във фабриката е 19 години, и много амбициран, което определено личи. Качеството на сглобката при H6 не отстъпва на това, което сме свикнали да виждаме при европейските или азиатски автомобили. Няма разминаващи се елементи или пък различни по големина хлабини. Едно просто отваряне и затваряне на вратите на автомобила показва, че в завода край Ловеч качеството е основен приоритет. Всъщност производственият процес в завода се осъществява по японски модел и по-точно по производствената система на Toyota - TPS (Toyota Production System). Мощна струя вода проверява дали уплътненията ще устоят на атмосферните условия Когато става дума за пътното поведение на H6, трябва да знаете, че той има комфортна настройка. Да, возията е приятно мека, но това се отнася и за поведението в завои. Лично на нас не допадна управлението, най-вече заради прекалено лекия волан. Спирачната система също може да бъде подобрена, тъй като педалът на спирачките се усеща леко твърд. Иначе, изолацията от шумове е сравнително добра, както и комфортът, който предлагат седалките. Дизайнът също е привлекателен, а оборудването дори на базовите версии е повече от богато. Което обаче се отразява на цената - от 38 990 лв. с ДДС. Снимки: Automedia.bg От автора на темата: Най - много се издразних обаче от коментарите под статията. Някакъв си анонимник обяснява, че искали с негов екип да снимат завода, но им отказали и от вътрешни хора били разбрали, че колите идвали цели и тук ги продавали така, а производствен процес имало само, когато от Литекс моторс изберат момент да пуснат репортери. Колко малоумен трябва да си първо да повярваш на подобна глупост и после да я пишеш по форумите, че на всичкото отгоре и да я повтаряш като папагал в няколко коментара.
-
Надежда за нов живот на родното машиностроене До 1989 г. машиностроенето е един от стожерите на родната икономика. България прави крайни продукти - от кранове, трактори и водни турбини до селскостопанска техника и инструменти. Къде е тайната на успеха? Фирмите имат осигурени пазари в страните от бившия соцлагер, а металургичните ни заводи им осигуряват евтини черни и цветни метали. 600 долара по това време е цената на 1 тон стомана на международните пазари, докато у нас е 320 лв. Това дава възможност да изнасяме по-евтини електрокари от тези на основните конкуренти - „Кларк“ и „Линде“. Разпадът на СИВ обаче се оказва фатален за сектора. Колосът ЗММ не успява да устои на конкуренцията на универсални машини от Далечния изток и продукцията му пада от 8800 струга през 1980 г. на 5014 през 1990 г. Надолу тръгват и останалите предприятия от бранша. Някои като „Тежко машиностроене“ - Радомир, наречен Завод за заводи, се държат трудно на повърхността. Други като холдинга „Балканкар“ отиват в историята, но има и отличници - една от гордостите на сектора е ЗММ-Сливен, който изнася в 54 държави. През м.г. предприятието е произвело 710 металорежещи машини или почти толкова, колкото през 1989 г. Те обаче са несравними по качество с това, което е правено в миналото. В своя поредица „Преса“ вече ви представи настоящото състояние на някои от иконите на химията и металургията, както и възможностите за развитието им чрез модернизация и технологии. Сега ви предлагаме поглед към машиностроенето, което има една голяма надежда - автомобилната индустрия и производството на компоненти за нея. България стои все по-добре на автомобилната карта на Европа. Само с един завод за леки коли край Ловеч това звучи пресилено, дори налудничаво. Но преценете сами: най-престижният сектор в машиностроенето вече е представен от над 40 компании, в които са заети 20 000 работници и чиято годишна продукция достига 1,8 млрд. лв. У нас се майсторят най-различни части - от електроника и части за двигатели до седалки и тапицерии. Почти няма голям производител, който да не влага в моделите си детайли с надпис Made in Bulgaria. Особено големи поръчки валят от „Фолксваген“, БМВ, „Рено“ и „Ауди“. По соцвреме България се опита да се вклини прибързано сред големите играчи в автомобилостроенето. Без сериозна подготовка на научноизследователски звена и без заводи за части идеята беше у нас да се сглобяват коли на чужди производители и да се пласират в държави, с които страната имаше добри отношения. Най-известните модели бяха „Булгаррено“ 8 и 10, асемблирани в края на 60-те години в Пловдив по договор с френската компания „Рено“. Към него прибавяме и спортния „Булгаралпин“, от който бяха произведени лимитирани бройки по същата схема. Успоредно вървеше и друга авантюра - в завод „Балкан“ в Ловеч се сглобяваха модели „Фиат“ под името „Пирин“. И това бе за кратко. Поточните линии в Ловеч се оказаха успешни, но за друга легендарна марка - съветския „Москвич“. От 1967 до 1990 г. там се монтираха над 300 000 коли. Последният опит да „покажем мускули“ бе през 1995-1996 г., когато в бившия завод за дизелови двигатели във Варна се сглобиха 2200 бройки „Роувър Маестро“. За жалост британците избраха лош момент за инвестиции - при правителството на Жан Виденов, въвлякло страната в тежка финансова криза. От началото на века страната ни постепенно започна да привлича чуждестранни компании, произвеждащи автомобилни части. Магнит се оказа съчетанието между евтина работна ръка, ниски данъци и стабилна валута. Особено добре е представен подсегментът „Кабели и кабелни системи“. В Карнобат и Мездра японският гигант „Сумитомо електрик“ прави части за „Фолксваген“, „Ауди“ и „Шкода“. Друга корпорация от Страната на изгряващото слънце - „Язаки“, произвежда в Ямбол и Сливен кабелни системи за „Рено“ и „Форд“. В групата влизат и турските компании „Нурсан отомотив“ и „Атес“. Най-новата инвестиция е на германския производител на кабелни системи „Нексанс аутоелектрик“, която ще строи завод в Плевен. Сред клиентите Ӝ са „Даймлер“ и „Дженеръл мотърс“. Друга германска компания - „Бер-Хелла термоконтрол“, вече гради халетата си в икономическата зона Божурище край София. Там ще се правят уреди за управление на климатични инсталации на автомобили. Ще има и развоен център. Първоначалната инвестиция се оценяваше на 42,5 млн. лв., но скоро стана ясно, че сумата ще набъбне двойно. „Бер-Хелла“ работи за „Фолксваген“, „Дженеръл мотърс“, „Ауди“, както и за елитни марки като „Порше“, „Ламборгини“ и „Бугати“. „Витте аутомотив“, също германско дружество, е в процес на изграждане на завод за заключващи системи за автомобили в Русе. Първият етап на проекта е за 10 млн. евро и ще бъде готов догодина. Междувременно немалко от работещите у нас компании се разширяват. Френската „Монтюпе“ (цилиндрови глави и носачи) строи ново хале с площ 10 000 кв. м в Русе. Южноафриканската компания ALC довършва завод в Ихтиман, където ще се правят тапицерии за седалки на „Мини Купър“. Това е втората производствена мощност на дружеството след тази в Мусачево. Турската „Стандард профил“ разширява производството си в Стара Загора, след като спечели поръчка за каучукови уплътнители за „Опел“. „Теклас холдинг“, пак от Турция, планира трети завод за каучукови и пластмасови изделия край Кърджали. С толкова добре представен сектор е въпрос на време в България освен в Ловеч отново да се сглобяват автомобили. Преди десетина години изтървахме на косъм „Хюндай“, сега ухажваме усърдно германски компании. БМВ или „Мерцедес“? А защо не и двете! Части от България има дори в „Порше“. В индустриалната зона край Раковски се правят метални изделия за скъпите спортни автомобили Българо-китайска инвестиция за 80 млн. евро Единственият (засега) завод за сглобяване на автомобили у нас е съвместната инвестиция на българската „Литекс моторс“ и китайската „Грейт уол“. Предприятието край ловешкото село Баховица бе открито през февруари 2012 г. Инвестицията е над 80 млн. евро. От автомобилната фабрика излизат модели от марката „Грейт уол“, като над 200 работници се грижат за пълната им окомплектовка. Най-новият модел е джипът Great Wall H6. През есента на м.г. първите партиди пикапи от „Литекс моторс“ потеглиха към европейския пазар. Дружеството изнася за Италия. Максим Клейтман, акционер в „Бесттехника - Тежко машиностроене“ - Радомир: Не бива да оставаме извън големите проекти Максим Клейтман За да се възроди машиностроенето, трябва да се осигури максимално участие на български фирми в големите инвестиционни проекти. Ще дам пример с „Южен поток“, където ще се изграждат компресорни станции и там биха могли да участват наши производители. Но за да стане това, трябва да има модел за участие на български подизпълнители. В момента „Девня цимент“ прави нова производствена линия, но проектът се изпълнява от китайска фирма под ключ. Той се прави от техни специалисти. Китайски са дори болтовете и гайките. За да не се получава така, държавата ни трябва да поставя условия пред инвеститорите, когато им дава преференции. Ще дам и още един пример. В проекта за АЕЦ „Белене“ се предвиждаше 30% българско участие, но се говореше предимно за строителство. В Чехия обаче, където също има план за разширение на АЕЦ „Темелин“, е предвидена 70% локализация. Така че цялата чешка индустрия се готви за този проект и той ще бъде един импулс за нея. Трябва ясно да се определят и националните приоритети. Това ще даде пазарна ориентация на компаниите от сектора. Те ще могат да планират производството си 5-6 г. напред. А не днес да казваме, че ще правим пристанищен терминал, а утре - яхтено пристанище. Индустрия не се прави от днес за утре. Сега правителството се готви да освободи вноса на инвестиционно оборудване от ДДС. Мисли ли някой какво ще стане с нашите производители на машини? ЗММ-Сливен, който произвежда широка гама от стругове, изнася в 54 държави. В края на миналата седмица изпълнителният директор на дружеството - Георги Добрев, получи престижната награда „Атанас Буров“ за индустриално управление Старозагорски завод изнася цялата си продукция Христо Христов Машиностроенето бе сред първите засегнати от кризата отрасли, но и първо може да излезе от нея, ако работи за различни пазари по света. Това е мнението на Антон Андронов, член на съвета на директорите на „Холдинг Загора“. В структурата му е „Хранинвест-Хранмашкомплект“ АД, водеща фирма в машиностроенeто, производител на машини за хранително-вкусовата промишленост. В момента дружеството работи почти изцяло за износ, като близо 90% от продукцията му е предназначена за външни пазари. Сред клиентите има компании от Англия, Германия и САЩ. През м.г. оборотът на компанията е около 30 млн. лв. В завода са заети близо 600 души, по-голямата част от хората са с висше инженерно и средно техническо образование. Холдингът има завод в Стара Загора и филиали в Килифарево и Момчилград, където се извършват десетки дейности като механична обработка на прецизни и конвенционални детайли, механична обработка на едрогабаритни детайли, изработка на едрогабаритни заварени стоманени конструкции и неръждаеми резервоари. От 80 000 сега правим около 1000 електро- и мотокари годишно Леонора ЛЕКОВА Българската фирма „Димекс лифт“ произвежда край Минск електрокари съвместно с белоруския частен завод „Амкодор“. „Балканкар холдинг“ отдавна е спомен, но няколко фирми правят опит да възродят родното каропроизводство. Битката за оцеляване е огромна, казва Петър Петров, управител на най-голямата - „Балканкар рекорд“ в Пловдив. По думите му за м.г. в страната са произведени около 1000 електро- и мотокари. „Проблемът е, че разходите ни непрекъснато растат и така ставаме неконкурентни. В момента нашите цени са равни на японските и на корейските и са много по-високи от китайските. Държим се благодарение на сложни комбинации, които правим между вътрешния и външния пазар, но за нови технологии трудно се намират пари, признава Петров. Със зъби и нокти се бори за клиенти и пловдивската фирма „Димекс лифт“ ООД, която развива съвместно производство в близост до Минск с белоруския частен завод „Амкодор“. През м.г. произведохме 180 електрокари, каза управителят Костадин Димитров. Оттук се внасят хидравликата, управлението и електромоторите, а в Белорусия се правят тежестите, рамата и покривът на карите. По-ниските транспортни разходи също гарантират добри цени на готовата продукция, която е насочена основно към Русия и Беларус. Едва ли обаче някога ще се върне старата слава. До 1989 г. машиностроителният гигант „Балканкар“ е №1 в света в производството на кари с около 80 хил. машини годишно. През 1992 г. в холдинга работят 55 000 машиностроители. След разпадането му повечето от предприятията са закрити. Така през 1997 г. производството пада на 1800 кари, а някогашният гигант изпада от световните класации. Това е краят на една империя, която се превръща в купчина неработещи предприятия. Как може да помогне държавата на каропроизводителите? С комплексни мерки, казва Петър Петров. Но най-важното, от което имаме нужда, е спокойствие. „Да няма скандали, да няма афери, защото лошият имидж отблъсква клиентите. По-високи цени дават и доставчиците. В интернет скрито-покрито няма и като видят, че тук искат пари за всяко нещо, си казват: „Я по-добре да отида другаде.“ Така няма нито клиенти, нито инвеститори. (в. Преса, печатно издание, брой 34 (740 от 4 февруари 2014) От написаното се вижда, че съвсем малко ни трябва за да започнем отново да произвеждаме автомобили. Не знам какво става със следващите етапи от изграждането на завода в Баховица, но съм сигурен, че след като бъдат готови цех Заваръчен и цех Бояджийски преспокойно Литекс моторс могат да пристъпят към изграждане на Център за развойна дейност. Наличието на толкова производители на автомобилни части в страната ще улесни максимално производството на автомобили.
-
Пърформънс тест на Haval H8 2.0Т 6 АТ
тема отговори на bobonikolov's bobonikolov в Hover CUV / H3 / H5
Благодаря за информацията :-). Както се вижда от клипа китайците не си поплюват и почват да правят все по - качествени модели. Имам чувството, че пуснат ли двата Хавала - Н6 и Н8 на европейският пазар редица производители в тоя сегмент като Фолксваген може да почнат да губят пазарни позиции. -
Предлагам Ви обстойно видео на пълен тест на новия Хавал Н8 2.0Т 6АТ, който е тестван на скоростна тестова писта на Грейт уол моторс в Китай. От описанието на видеото, което е на английски става ясно, че теста е бил в следните части: 1. Ускорение ( 40 - 180 км/ч, 0-100 км/ч в режими Еко и Спорт) 2. Тест за максимална скорост; 3.Тест за маневреност; 4.Тест Borg Warner TOD(Torque on Demand) ( каквото и да означава това) 5. Тест за изкачване на наклон с 60 % (31 градуса) на 1 - ва скорост с 2000 оборота в минута и асистент за спускане по наклон; 6. Тест на биксеноновите фарове, фаровете за мъгла като адаптивни светлини ( или нещо от сорта) и AFS тест ( каквато и да е тази система) 7. Тест на чистачките на предните фарове, тест за излищни вибрации на двигателя както и шумов тест. За съжаление видеото е на Китайски и не се разбира какво се говори вътре. От коментарите под клипа обаче става ясно, че Н 8 е трябвало да бъде пуснат в продажба до сега, но са открити някакви минимални дефекти точно преди пускането в продажба на модела и то е отложено за около 20 април в Китай. Според мен това означава, че може би след около година, година и нещо ще бъде пуснат в производство и в България. Да се надяваме това да се случи скоро :-) https://www.youtube.com/watch?v=YZ9Nv1-Offw
-
"Видях Great Wall" - къде и кога? Ако може и снимка :)
тема отговори на bobonikolov's feikot в Общи приказки
В община Гърмен от приблизително година движи сив H5. Туристическото влакче също е на базата на H5, В и К движат няколко Стийда, същото правят и Горското стопанство. -
На мен лично ми е интересно какъв ще е този нов бензинов двигател със 150 конски сили.
-
Първият български Great Wall H6 се продава на търг
тема отговори на bobonikolov's poroinik в Hover CUV / H3 / H5
Уважаеми госпожи и господа, скъпи приятели, В началото на м. март 2014 г., „Литекс моторс” АД – българският производител на автомобили, пусна на пазара новия модел високопроходим автомобил на Great Wall – Н6. Както ние, екипът на „Литекс моторс” АД, така и много от Вас – нашите приятели и почитатели на марката Great Wall, очаквахме с нетърпение слизането на първия автомобил H6 от производствената линия в с. Баховица, край Ловеч, в края на месец декември 2013г. Подтикнати от повишения интерес, предизвикан от предстоящата премиера на новия модел, ние решихме първият произведен автомобил от новия модел да бъде предложен за продажба чрез публичен търг, който да се проведе ”онлайн”. Искахме по този начин един от Вас да купи, на предложена от него цена, един изключителен автомобил с потенциална колекционерска стойност – не просто първият произведен в България Great Wall H6, а първият високопроходим автомобил, произвеждан някога в нашата страна. За съжаление в търга се включиха и някои недобросъвестни участници, които се опитаха да опорочат добрата идея на организатора. Един от участниците, например, се регистрира с 4 различни профила, наддавайки общо 305 пъти. В някои моменти от развитието на търга е наддавал дори „срещу себе си” – т.е. срещу някои от „участниците”, чиито привидни профили са създадени от самия него. Независимо от това, искаме да уверим всички участници, които наддаваха в търга добросъвестно и с искреното намерение да станат собственици на първия произведен в България Great Wall H6, че „Литекс моторс” АД, ще направи необходимото, за да защити техния интерес. Ето защо, съгласно общите условия на търга, ще продължаваме да се свързваме последователно с участниците в търга, спазвайки поредността от по-високи към по-ниски крайни цени, предложени от тях. На всеки един от тях ще бъде предоставена възможността купи автомобила на предложената от него цена. Щастливецът, който купи автомобила със сериен номер „0000001“ ще получи и специален подарък – картина за спомен със снимка на екипът от млади специалисти, произвел неговият автомобил с подписи от самите тях. Очаквайте скоро допълнителна информация от нас. Поздрави, Екипът на „Литекс моторс” АД, София 11.03.2014г. -
Интересното е друго - този модел го няма въобще в сайта на Грейт уол.